サーモグラフィによる工程検査システムの開発
キーワード:熱画像,サーモグラフィ,画像処理,ホットメルト,温度分布,自動判定
飲料用のペットボトルや缶の梱包は、ホットメルトを用いた接着を行うことで段ボール箱を形成する「パッケージ成形ホットメルトライン」という工程で行われている。従来の良否判定装置は、可視画像を用いて行っており、塗布直後のホットメルトの形状しか検出できず、実際の接着状態の判定ができない課題があった。そこで、可視画像の代わりに熱画像を取得可能な赤外線サーモグラフィを用いて、塗布後に段ボールを張り合わせた状態でのホットメルトの形状を収集して、それを画像処理することにより良否判定が行えるシステムを開発した。
1.はじめに
人件費の高騰,品質の安定などの様々な要因により,生産現場における自動化の要求が増えてきている。生産の自動化において,ワークの位置決めや検査などで人の目の代わりとなる画像処理技術が重要な要素となっている。当社においても生産に適用するための画像処理技術の開発を行っており,実際の生産現場にて利用している。
生産の自動化を進めていく中で,食品や飲料,鉄鋼,化学,自動車,電気電子など温度の計測を必要とする対象がある。温度計測の方法として熱電対を用いた接触式の温度計測が多く用いられているが,食品など非接触で離れた場所から温度を測定しなければならない場合がある。非接触による温度計測の方法として,放射温度計が以前から用いられているが,放射温度計では計測箇所は点での計測となるため温度分布を求めることは難しい。点による計測ではなく温度分布による面の2次元データの計測ができると,温度ムラや局所的な温度異常なども分かり品質の安定が望める。
従来から,可視光カメラのように面である2次元データとして温度計測可能な赤外線サーモグラフィがあるが高価であった。しかし近年,赤外線サーモグラフィは比較的安価な製品を手に入れることができるようになってきた。また大きさについても生産現場で適用可能なサイズであり,データを取得するためのインターフェースも,可視光の画像処理で用いられている汎用のカメラ接続インターフェースを持つ製品が入手可能となってきている。
そこで,赤外線サーモグラフィと画像処理技術を組み合わせ,塗布したホットメルト検査に有効な「サーモグラフィ良否判定システム」を開発した。
2. パッケージ成形ホットメルトライン
開発した赤外線サーモグラフィを用いた良否判定システムの適用対象である「パッケージ成形ホットメルトライン」について説明する。パッケージ成型ホットメルトラインは主に運搬用段ボール箱(飲料やトイレタリー商品)を閉じるために160℃程度のホットメルト(糊付け)を塗布し接着を行うラインである。
飲料の缶ケースの場合,3面(左右面合計16箇所程度,上面6箇所程度)にホットメルトを塗布し接着を行う。1分間に60箱から100箱のスピードで生産されており,繁忙期になると24時間稼働を行っている工場も多い。ホットメルトを塗布し段ボールを接着する工程では,塗布による不良が発生する場合がある。発生する不良モードとしては,「位置不良」,「のり不足」,「のり欠け」,「のり過多」,「のり飛び」,「圧着不足/温度不足」,「のり切れ」がある。
現在は検査方法として主に以下の方法がある。
① 抜き取り目視検査
② 可視光カメラでの確認
①の場合は30分に1回程度抜き取り検査を行っている。接着面を剥がし,糊付け部分の接着具合を確認,糊が塗布されている長さ確認などを行っており,不具合を発見した場合,30分前までの生産数量分すべてをチェックする必要があり,それらの人的コストや作業時間を要する。
②に関しては,ホットメルト接着部分が紙の間にあるため,可視光カメラで確認しようとすると箱を閉じる前に判定を行う必要がある。この場合は接着前の確認になり,実際,接着できたかどうかの確認はできない。
これら従来の検査方法では課題があり,パッケージ成形ホットメルトラインでは検査工程において生産性と品質の向上が期待されていた。
3. サーモグラフィ良否判定システムの構成
これらの課題を解決するため,接着後の段ボール表面温度を測定し,ホットメルト位置や数量,面積等を検査し判定することで,ラインを止めることなく接着後の全数チェックを可能とする「サーモグラフィ良否判定システム」を開発した。パッケージ成形ホットメルトラインにサーモグラフィ良否判定システムを導入するにあたり,必要となるシステムの構成を図1に示す。
システムは3台のサーモグラフィとパネルコンピュータおよびサーモグラフィへの電源供給も兼ねるPower over Ethernet(PoE)ハブで構成される。3台のサーモグラフィを用いることで,段ボールの3面に塗布されたホットメルトの2次元熱画像を取得することができる。動作としては,まずサーモグラフィによりホットメルトが塗布された段ボール表面の2次元温度データ(以下2次元熱画像)を取得する。
図2に段ボールに塗布したホットメルトの2次元熱画像をサーモグラフィで取得した例を示す。サーモグラフィで取得した2次元熱画像データは,PoEハブを通してパネルコンピュータに渡される。パネルコンピュータは,サーモグラフィで取得した2次元熱画像データを,後述するアルゴリズムに基づき判定処理し,また本システム全体のコントロールを行う。
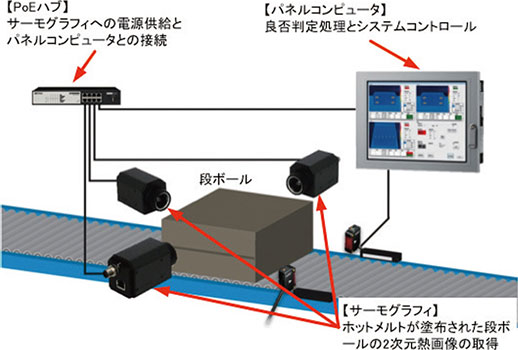
図1 システム構成図
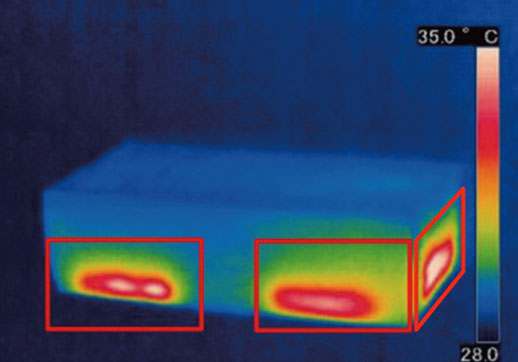
図2 段ボールに塗布したホットメルトの2次元熱画像
4. パッケージ成形ホットメルトラインにおける検査技術
パッケージ成形ホットメルトラインにおける検査(良否判定)は,ホットメルトを塗布し,段ボールを張り付けた状態で行う。通常の可視光カメラでの輝度情報と異なり,サーモグラフィを用いることで2次元熱画像を取得することができ,放射温度計とは異なり面として温度情報が得られる。ホットメルトを塗布し段ボールを張り合わせた状態で,伝熱による段ボール表面でのホットメルトの間接的な温度分布を測定することが可能となるため,得られたデータを元に画像処理を行うことで,実際に接着したホットメルトの塗布位置と範囲およびその温度分布を求めることができ,ホットメルト塗布の良否判定を行うことができる。以下で各モードの検査方法を紹介する。
4.1 各不良モードの検査方法
ホットメルトを段ボールに塗布した状態で,塗布したホットメルトの形状による不良の種類の模式図を図3に示す。
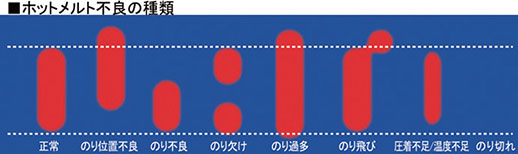
図3 ホットメルト不良の種類模式図
不良モードとしては,「位置不良」,「のり不足」,「のり欠け」,「のり過多」,「のり飛び」,「圧着不足/温度不足」,「のり切れ」がある。ホットメルトの塗布状態は,サーモグラフィから得られた1枚の2次元熱画像に対して以降4.1.1から4.1.3に示す3つのアルゴリズムを用いることで,良否判定および各不良モードの検出が可能となる。
4.1.1 位置不良,のり飛び不良
位置不良,のり飛び不良の例を図4に示す。位置不良は通常塗布されるべき位置からずれた場所に塗布されてしまった不良である。のり飛び不良は,塗布されてはいけない場所に塗布された不良である。これらの不良モードは,塗布されてはいけない場所に塗布されているという点で良否判定アルゴリズムとしては共通の処理にて可能となる。良否判定の方法について示した模式図とその処理手順のフローチャートを図5に示す。
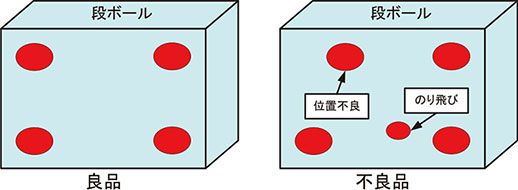
図4 位置不良,のり飛び不良模式図
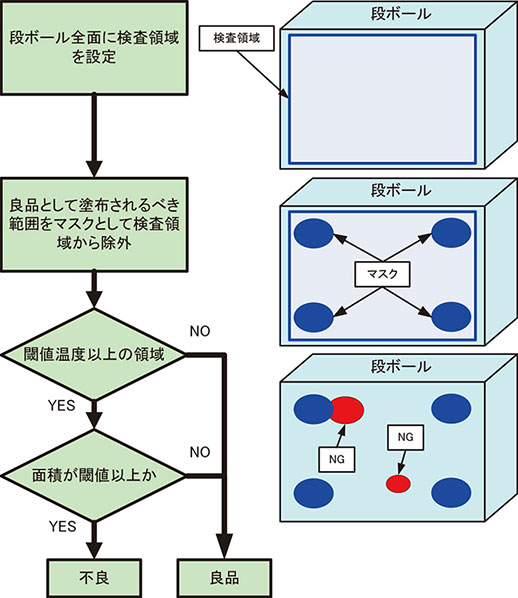
図5 位置不良,のり飛び不良の判定フローチャート
2次元熱画像を元に,良品として塗布されるべき範囲をマスクして検査領域から除外した残りの領域に対して温度で閾値を設定してホットメルト塗布領域を抽出し,その面積を求め良否判定を行っている。これにより,単純な温度での判別ではなく温度分布を元にした判断が可能となり特にのり飛び不良の検出が容易に可能となっている。
4.1.2 のり不足,のり過多,圧着不足/温度不足,のり切れ不良
のり不足,のり過多,圧着不足/温度不足,のり切れ不良の例を図6に示す。のり不足不良は,ホットメルトの量が少ない不良であり,のり過多不良は,逆に多く塗布された不良である。圧着不良は,塗布後に段ボールを折り曲げて張り合わせた際に圧着が不足していて隙間が生じてしまい接着力不足となる不良であり,温度不足不良は,塗布したときのホットメルトの温度が低いため流動性が低下し,段ボールを折り曲げて張り合わせてもホットメルトが広がらず接着力不足となる不良である。のり切れ不良はホットメルトが塗布されていない不良である。これらの不良モードは,塗布されたホットメルトの温度と面積を元に判定が可能であり,共通のアルゴリズムで処理が可能である。良否判定の方法について示した模式図とその処理手順のフローチャートを図7に示す。
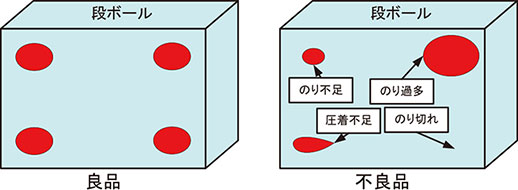
図6 のり不足,のり過多,圧着不足/温度不足,のり切れ不良模式図
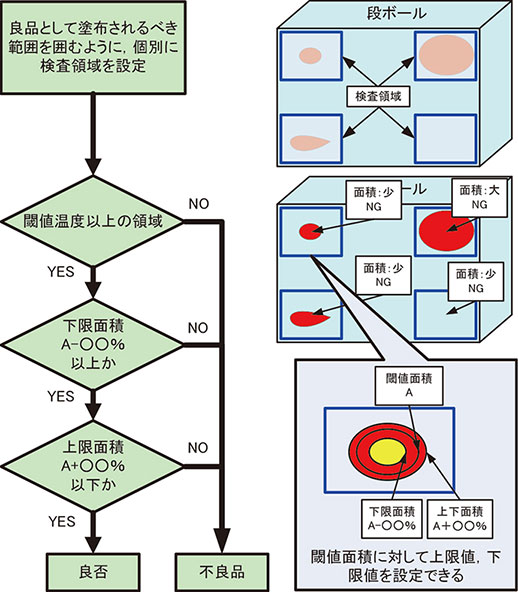
図7 のり不足,のり過多,圧着不足/温度不足,のり切れ不良の判定フローチャート
2次元熱画像を元に,画像処理にて温度の閾値でホットメルト塗布領域を抽出し,個別の検査領域ごとのホットメルト塗布面積を算出する。求めた個別の検査領域ごとの面積値から良否判定を行うが,良品の面積値にばらつきが存在するため,面積の閾値に上限値,下限値を設けその範囲内であれば良品とする。単純な温度判定のみでは,本来は不良とすべき「閾値温度以上だがホットメルト塗布領域が小さい場合」に良品と誤判定してしまうが,面積を用いることで誤判定をなくすことができる。また,閾値温度以上のホットメルト塗布面積のばらつきを考慮した判定が可能となる。
4.1.3 のり欠け不良
のり欠け不良の例を図8に示す。のり欠け不良は,ホットメルトの塗布された領域が途中で分断されてしまっている不良である。途中で分断されている状態は,ホットメルト塗布装置における異常であるため不良として検出する必要がある。良否判定の方法について示した模式図とその処理手順のフローチャートを図9に示す。
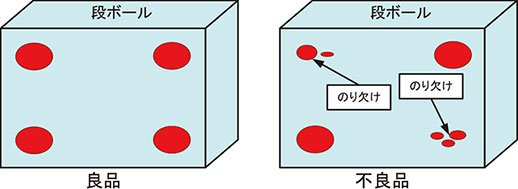
図8 のり欠け不良模式図
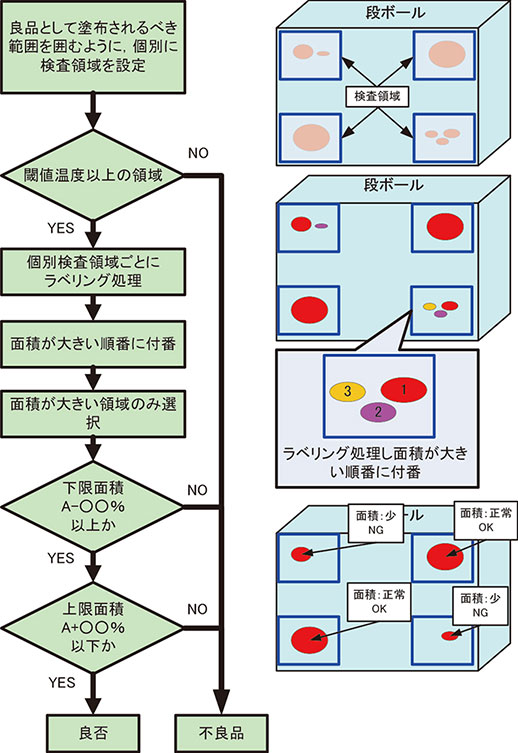
図9 のり欠け不良の判定フローチャート
2次元熱画像を元に,画像処理にて温度の閾値でホットメルト塗布領域を抽出し,個別の検査領域ごとのホットメルト塗布面積を算出する。ただしのり欠け検査では,検査領域内に複数の分離したホットメルト塗布領域が存在する。そのため単純に温度閾値を元に求めた面積値では,複数領域面積の和となり,ホットメルト塗布領域が分かれていても良品となってしまう場合がある。そこで,求められたホットメルト塗布面積領域に対してラベリング処理を行う。ラベリングした各領域に対して面積が大きい順に番号を付番し,個別の検査領域ごとに一番大きな面積を持つホットメルト塗布領域のみを選択する。選択した領域を元に面積値で判断することで複数のホットメルト塗布領域に分かれた場合でも良否判定を行うことができる。この時,面積の閾値に上限値,下限値を設定することでホットメルト塗布におけるばらつきを考慮した判定が可能である。
4.2 トレンド表示機能
前記4.1章の各不良モードの検査方法で述べた「閾値温度」の設定を行う補助ツールの1つとして,トレンド表示機能がある。2次元熱画像に,温度変化を知りたい領域を設定することで,その領域の温度変化を,数値データおよびグラフとして表示することができる。求めた温度のトレンドから,検査設定における温度閾値の目安を求めることが可能となる。トレンド表示機能では以下の設定が可能である。
① 領域設定は,矩形領域を10箇所まで設定可能。
② 各領域のモニタ温度として,領域内最高温度or最低温度or平均温度を選択し,そのトレンドを表示することが可能。
③サンプリング周期は1秒~100秒が選択可能。
図10はトレンド表示機能の例として,ホットメルトの自然冷却状態を測定したものである。
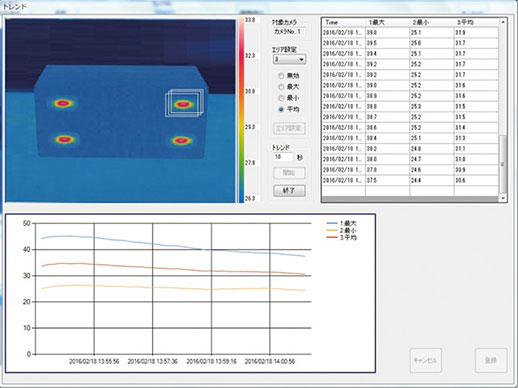
図10トレンド表示機能
ホットメルトは,最初約45℃の状態から,周囲温度約24℃に向かって,徐々に自然冷却している。図10におけるトレンド表示の設定は以下である。
- 領域設定は1,2,3の3箇所。特定のホットメルトおよび周囲を含んでほぼ同一領域に設定(図10内白枠)。
- 各領域は,領域1(最高温度),領域2(平均温度),領域3(最低温度)をモニタとして選択。
図10のトレンド表示から,領域3(最低温度)は約24℃で,これは周囲温度を意味しほとんど変化していない。領域1(最高温度)は,約38℃で,ホットメルト温度がここまで冷却したことが分かる。
本例では特定のホットメルトの冷却過程を測定したが,領域設定は10箇所可能なので,例えば他のホットメルトの温度変化も測定し,比較することも可能である。
このように,トレンド機能を用いることにより,2次元熱画像中の,背景/物体の各部位の温度変化を,簡便に知ることができ,検査設定における閾値温度を設定するための指標とすることができる。
5. サーモグラフィ良否判定システムの現場への適用
開発したサーモグラフィ良否判定システムは基本検査機能として,以下の(1),(2)を,付加機能として以下の(3),(4),(5)を有する。
(1)良否判定
ホットメルトの位置,たれ,飛び散り,面積の増減等の判定
(2)検査速度・データ保存
100箱/分に対応した検査速度,および結果画面のスクリーン保存,検査結果の数値をCSVデータに保存
(3)品種設定
15品目の品種設定
(4)検査位置補正
段ボールの位置あわせのための判定エリアの位置補正機能
(5)温度基準差分判定
基準との温度比較による,朝晩の温度差や季節による温度差の影響低減
これらの基本機能,付加機能によりパッケージ成型ホットメルトラインにおけるホットメルト塗布検査の生産性向上および品質向上を実現する。
実際にパッケージ成形ホットメルトラインに導入した際の判定画面を図11に示す。図11よりホットメルトの温度を段ボールの表面からサーモグラフィで測定することで,2次元熱画像にてホットメルト塗布による接着部を確認できる。サーモグラフィ良否判定システムにより接着部の面積を求めることで,確実に接着されているか,また,ホットメルト塗布量が適当かどうか全数チェック可能となる。そのため,従来の人による抜き取り検査を行う必要がなく,ホットメルト塗布検査の時間短縮に大きく貢献できる。
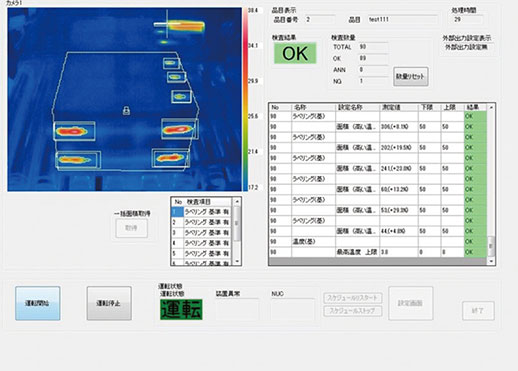
図11 判定画面
6. アプリケーションの展開例
開発したサーモグラフィ良否判定システムは,食品/飲料/鉄鋼/化学/自動車/電子・電気等の市場における幅広いアプリケーションに展開できる。以下にその一例を示す。
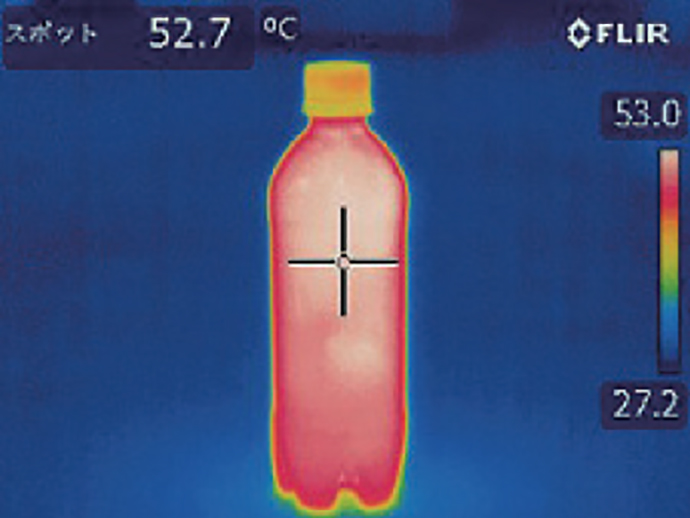
成形品の品質管理
ペットボトル成形時の温度管理
形状検査
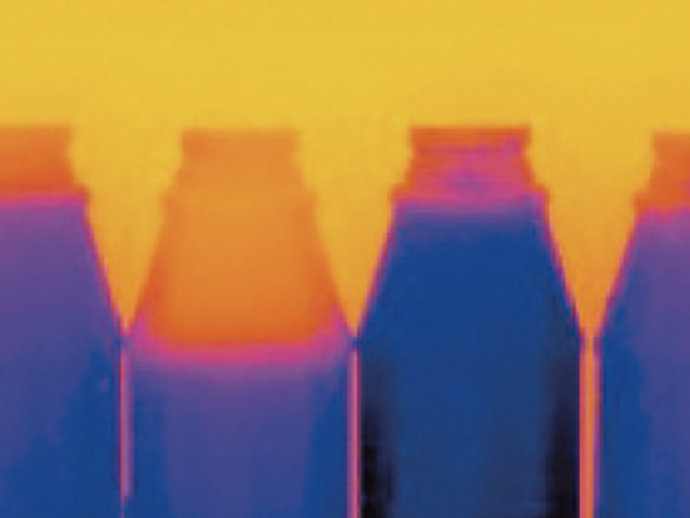
充填物容量検査
飲料の充填容量可否検査
ガスボンベのガス充填有無検査
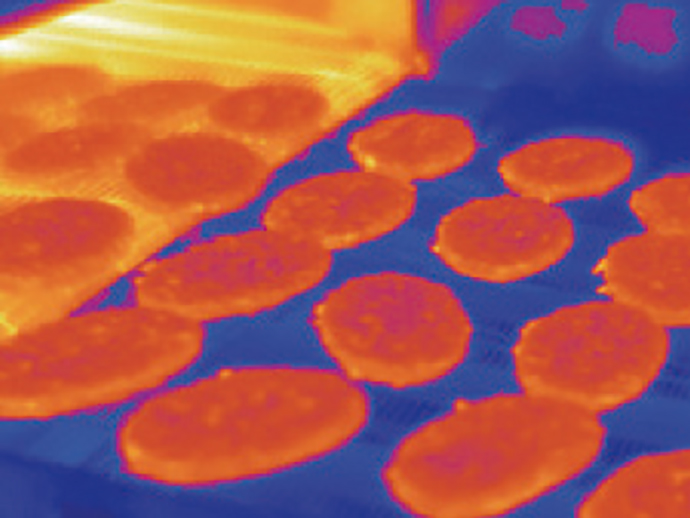
食品製造時の品質管理
製造時の温度管理(面積・長さ・幅)
冷凍食品の解凍時の温度管理
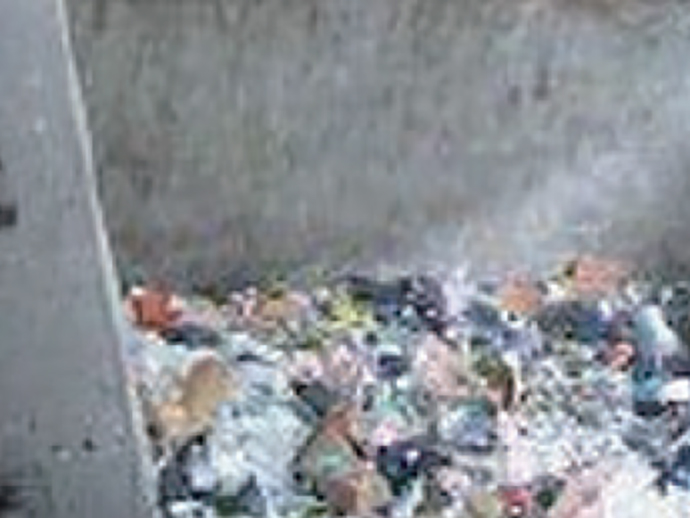
温度上昇によるトラブル監視
ゴミピットの温度異常監視
設備の温度監視
7. おわりに
赤外線サーモグラフィから得られるデータは2次元データであるため,可視光カメラで用いられている画像処理技術をそのまま適用可能である。また本文で記載したパッケージ成形ホットメルトラインでの検査への適用のように,可視光では不可能であった温度分布を元にした画像処理が可能となり,今後生産現場だけでなく様々な用途でサーモグラフィから得られる2次元熱画像を用いた画像処理技術の利用が広がると考えられる。
<参考文献>
(1) 吉田 慎吾,診断に使われる赤外線サーモグラフィ,画像ラボ,2013年8月号
<著者所属>
越口 一敏 アズビルトレーディング株式会社 営業推進本部安全営業部
瀬戸 新一郎 アズビル株式会社 技術開発本部基幹技術開発部
金原 圭司 アズビル株式会社 技術開発本部基幹技術開発部
この記事は、技術報告書「azbil Technical Review」の2016年04月に掲載されたものです。