MEMSセンサの能力を最大限に発揮させるセンサパッケージング技術
キーワード:MEMSセンサ,センサパッケージング,計測と制御
アズビルは計測と制御の技術の要となるMEMSセンサ開発において,MEMSセンサチップ開発技術とセンサパッケージング技術の両者を保有することにより,他社が容易に追従できない優れた計測制御機器の開発を可能としている。センサパッケージングにおいては,ウエハ面内の膜厚のバラツキや金属と異なる線膨張率を有するといった製品化を行う上で不利となるMEMSセンサチップの特性を補完し,さらにMEMSセンサチップの材料が有する優れた特性を活かすことが重要である。本稿では,アズビルのセンサパッケージング技術について報告する。
1.はじめに
計測と制御の技術の要となるMEMS(Micro Electro Mechanical Systems)センサの開発において,センサパッケージングに特化した工法開発,生産設備開発を行い,安定した生産工程を実現させる生産技術はアズビルのコアコンピタンスの1つである。MEMSセンサチップはシリコン,ガラス,サファイアなどの材料に微細な機械的構造や電気回路を形成することで,圧力や流量などの物理量を精度よく計測することを可能とするが,そのためには材料のもつ機械的,熱的特性が計測精度へもたらす影響を最小限に抑制することが必要である。MEMSセンサチップは図1に示すような円盤状の薄板であるウエハ状態に加工された材料に一度に多量生産するため,ウエハ面上に施された金属膜や絶縁膜などの面内部位におけるわずかな厚みの違いにより, 個々のセンサチップの特性に変化を生じさせてしまうことがある。MEMSセンサチップに安定して高い計測精度を発揮させるためには,この材料特性の影響およびセンサチップ個々の特性の差異を吸収,調整し, 一定の性能に整えた上で計測機器に搭載することが重要である。
また,MEMSセンサのチップの材料の一種であるサファイアを使用したMEMSセンサチップでは,高耐熱性,高耐食性のように優れた材料特性を損なうことなく計測能力を発揮させることで,これまで計測が困難な環境下への適用が可能になるなど特徴的な計測機器を実現することができる。
アズビルではMEMSセンサチップやマイクロデバイスを物理的,電気的に計測機器製品の電気回路に接続しセンサモジュールにする技術をセンサパッケージング技術と呼んでいる。アズビルのセンサパッケージング技術は単に電気回路に接続させるだけではなく,製品化を行う上で不利となるMEMSセンサチップの特性を補完し,優れた特性を活かす計測機器の「センサ」としてモジュール化することを特徴としている。
MEMSセンサの開発において,MEMSセンサチップ開発技術と,このセンサパッケージング技術の両者を保有していることが,他社が容易に追従できない優れた計測制御機器の開発を可能としている。
本稿ではアズビルの保有するセンサパッケージング技術の一部について紹介する。
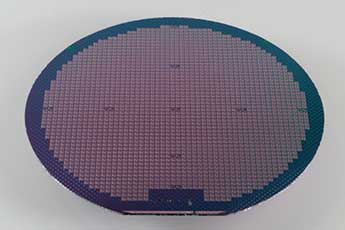
図1 シリコンウエハに形成したセンサチップ群の一例
2.MEMSセンサチップの製品適用における課題
センサパッケージング技術はMEMSセンサチップを均一の特性に整え,物理的,電気的に計測機器製品と接続することのできるセンサモジュールにする技術である。アズビルのセンサパッケージング技術の主な特徴である製品化を行う上でMEMSセンサチップの不利となる特性を補完し,優れた特性を活かす2つのケースを,実際の製品での課題をもとに説明する。
2.1 ピエゾ式圧力センサにおける課題
ここでは,ピエゾ式圧力センサを例にとり,2つの課題について説明する。
2.1.1 MEMSセンサチップの特性のウエハ面内分布の影響
プロセス流体の流量計測には,差圧式の流量計が最も多く用いられている。差圧式の流量計は,流体の流路にオリフィス(絞り弁)を設置し,圧力損失を故意に発生させ,オリフィスの上流・下流の圧力差,つまり差圧を検出して流量を演算する方式であり,液体,気体,高温・高圧流体など様々な流体の計測が可能であり,さらに故障しづらいなどの多くのメリットがある。差圧計測のためには,2台の圧力センサを使用する方法が最も簡単であるが,2台の圧力センサを使用しての圧力差の計測は,ウエハ面内分布に起因するセンサチップの特性の個体差により高い計測精度を得ることが困難という課題がある。
2.1.2 熱応力による温度特性の影響
シリコンウエハ上に形成されるピエゾ式圧力センサは高い分解能と安定した計測を可能とする。製品に搭載するためには,図2に示すようにセンサチップをステンレス等の金属材と接合することが必要であるが,熱膨張率の違いによる熱応力が発生し,計測精度に影響を与えてしまう。この影響を緩和する方法として,センサチップと金属部品の間の中間部材に熱膨張率の異なるガラス等を接合する手段を採用している。中間部材を接合したセンサを金属部品に接着剤で接合するが,設計上の制約により中間部材が応力緩和するための十分な長さを確保できない場合や,接着剤の硬化時に発生する応力が新たな課題となる場合もある。
従来の接着工法は,エポキシ系接着剤を使用して,135℃で加熱硬化させたあと,硬化時の応力を緩和させるために徐冷を行っている。エポキシ系接着剤は,硬化時に分子の重合により体積収縮を生じるが,表層部と樹脂内部に温度差が生じると硬化時の体積収縮差による残留応力が大きくなるため,徐冷により表層部と樹脂内部の温度差を小さくし,応力緩和を図っている。徐冷を行うことで従来の構造では十分な緩和効果が見られていた。
図3に示した流量計測制御機能付電動二方弁ACTIVAL™ に塔載されている圧力センサでは,センサモジュール小型化の要求により中間部材の長さを従来製品から2mm短くしている。従来製品より2mm中間部材を短くした新しい構造では同様の徐冷を行っても,図4に示すような無印加時の出力電圧の変化が発生し, 応力緩和効果が不十分であることが分かった。小型化と同時に高い計測制度が得られるセンサモジュール構造を実現するセンサパッケージング技術の確立が必要となった。
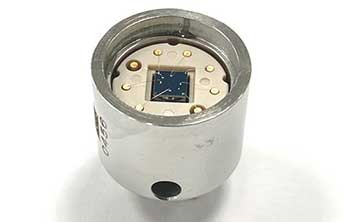
図2 ピエゾ式圧力センサモジュールの例
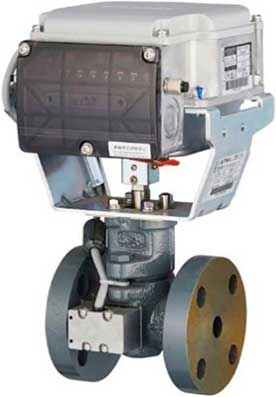
図3 流量計測制御機能付電動二方弁ACTIVAL
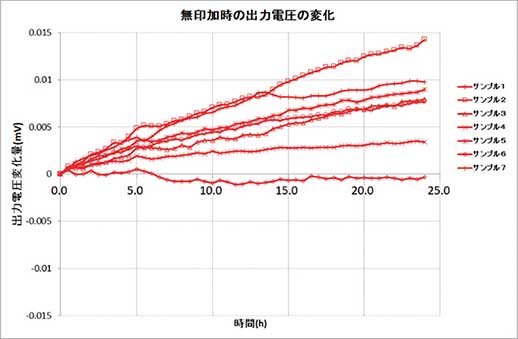
図4 24時間放置時の無印加時の出力電圧の変化
2.2 サファイアセンサにおける課題
次に,隔膜真空計にサファイアの高い耐熱性,耐食性という優れた特性を活かす上での課題について説明する。
2.2.1 サファイアセンサチップの高気密接合工法の確立
サファイア隔膜真空計に使用されるサファイア容量式圧力センサは材料であるサファイアの高い耐熱性,耐食性を活かし,半導体製造装置のプロセスで使用される腐食性ガス雰囲気など過酷な環境下での圧力計測に適用することができる。同真空計の外観を図5に示す。
しかしながら,このサファイアの優れた材料特性を損なうことなく製品のセンサモジュールとするためには,サファイア同様に高い耐熱性,耐食性を持った金属材料と接合するセンサパッケージング技術の開発が必要となる。
サファイア隔膜真空計では金属材料として高い耐熱性,耐食性を有するNi基合金を採用することとした。
サファイアセンサチップとNi基合金では熱膨張率が異なるため接合による熱応力の影響を緩和するために図6に示すようなセンサチップを薄膜状のNi基合金製のリングと接合させる構造を採用した。
接合には拡散接合が用いられるが,約1000℃の高温,高真空下で一定の圧力を接合面に均一に印加できる接続工程の確立が求められた(1)。
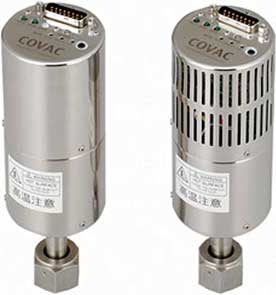
図5 サファイア隔膜真空計外観
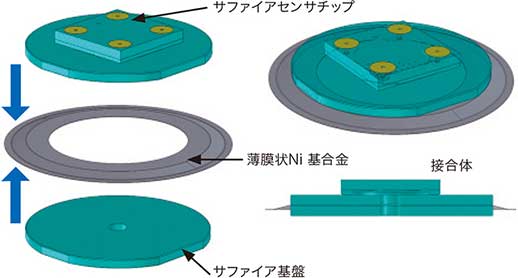
図6 サファイアセンサチップ接合体の断面模式図
2.2.2 高気密性接合の検査工程の確立
サファイア隔膜真空計はその名の通り真空に近い極めて低い圧力の計測に適用される計測機器である。
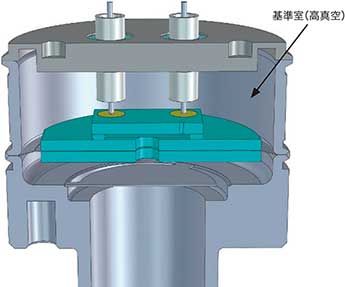
図7 サファイアセンサモジュールの断面模式図
図7に示す通りサファイアセンサチップを内在した基準室を高真空に保ち,測定雰囲気との差圧を計測することで圧力を計測している。当然基準室の一部を形成するセンサチップとNi基合金の接合体には高い気密性が必要となる。後工程に不適合品を流さないためにも,拡散接合されたサファイアチップとNi基合金との接合面の気密性を基準室に組み付ける前に検査できる工程開発が求められる。
基準室に組み付けられたあとに気密性が確保できていない場合は, 測定雰囲気の圧力とサファイアセンサチップの出力にミスマッチが発生するため,検査することは容易である。しかしながら基準室に組み付けられたあとに不具合判定されると,サファイアセンサチップだけではなく基準室およびセンサパッケージを構成するすべての部品を廃棄しなければならない。生産コストを圧迫させないためにも拡散接合後の気密検査工程の確立が求められた。
このように検査工程も含めて生産品の品質を担保することをアズビルではセンサパッケージング技術と定義している。
3.課題解決への取組み
2章で述べたMEMSセンサチップの製品適用における課題への取組みとして,製品化を行う上で不利となるMEMSセンサチップの特性を補完し,計測制度を向上させた事例を3.1で説明する。
一方,MEMSセンサチップのもつ優れた特性を損なうことなく,製品に搭載するためのセンサパッケージング工程,その検査工程の確立について,3.2で説明する。
3.1 ピエゾ式圧力センサにおける課題解決
ここでは,ピエゾ式圧力センサを例にとり,2つの課題解決について説明する。
3.1.1 センサへの差圧印加構造によるウエハ面内分布の排除
差圧計測において2台の圧力センサを使用するとセンサチップの特性の個体差により, 高い計測精度を得ることができないため, 1台の圧力センサでセンサチップの両面に圧力が印加される構造をとることにより精度向上を図っている。圧力センサモジュールの構造を図8に示す。2枚の受圧用ダイアフラムを有し,受圧部で受けた圧力がセンサチップに印加されるように圧力伝搬経路をパイプで繋ぎ,空間内に圧力伝搬用の液体を封入する構造となっている。
圧力伝搬用のパイプに太いパイプを使用すると,熱応力や圧力印加時の応力により,接合部が破損する恐れがあるため, 外径:φ0.45mm,内径:φ0.23mmの極細パイプを使用して連結している。パイプを直接ボディには接合せず,ワッシャと呼ばれる部材を中間に配置し,それぞれを溶接する構造をとることで接合の信頼性を確保している。
パイプ,ワッシャの溶接には,ファイバレーザーを用いており, 十分な溶け込みを確保しつつ,パイプ内を塞がない条件で照射を行っている。
ワッシャとボディは,湿度などによる劣化をさけるために接着ではなく抵抗溶接で接合しており,長期的な使用にも耐えられる構造となっている。圧力伝搬用の液体中に気泡が混入すると,圧力印加時の応答の遅れや温度影響によるセンサ出力の異常が発生するため,高真空化で液体の封入,封止を行うことで,気泡の混入を防止する工程を確立している。
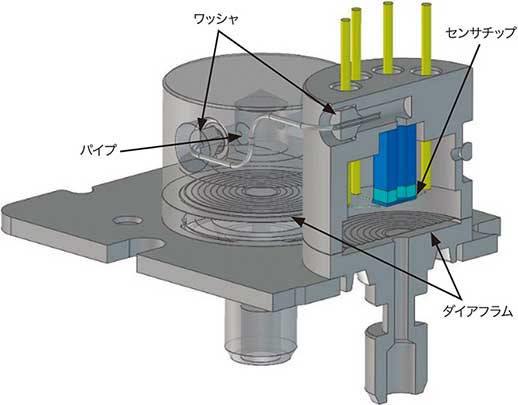
図8 圧力センサモジュールの断面模式図
3.1.2 センサチップへの熱応力排除
熱硬化型接着剤の硬化過程の体積は,加熱による温度上昇により液相状態で膨張し,硬化反応により樹脂の2次元的架橋が始まり,収縮を伴いながらゲル化点に到達する。ゲル化点で熱硬化型接着剤は液体から固体としての挙動に移行する。次に3次元的架橋に移行し,これの終点である硬化点に到達する。さらに冷却過程を経て室温に戻る。この過程の中で,固体化するゲル化点の体積と冷却後の体積との差が熱硬化型接着剤硬化時の応力へとつながる(2)。
接着剤での発生応力の低減を図るために,加熱硬化温度に着目した。図9において,液体から加熱された際に熱膨張しながら,つまり体積が膨張しながらゲル化点まで向かうことが示されているが,硬化温度が低くなれば硬化後までの体積変化量も低くなり,収縮応力を小さくすることができると考えた。従来の硬化温度135℃に対して,硬化温度を95℃とした際の無印加時の出力電圧の変化を図10に示す。硬化温度を下げることで硬化時の応力を緩和させ,無印加時の出力電圧の変化を低減できることが分かる。
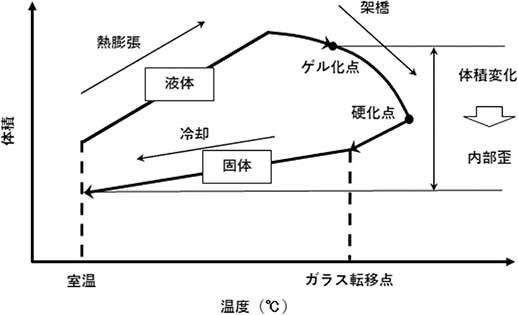
図9 接着剤硬化時の体積変化
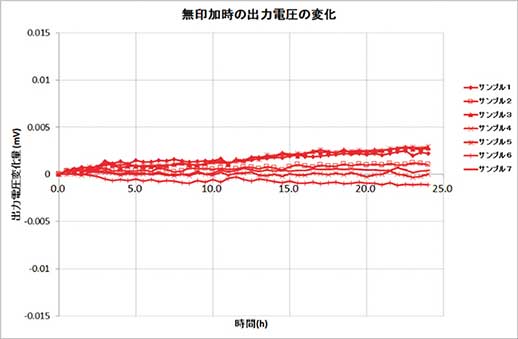
図10 24時間放置時の無印加時の出力電圧の変化
3.2 サファイアセンサにおける課題解決
次に,サファイアセンサにおける2つの課題解決について説明する。
3.2.1 高耐食性金属であるNi基合金との拡散接合
サファイアセンサチップとNi基合金の接合に用いられる拡散接合とは,同種または異種材料同士を材料の融点以下に加熱し,加圧することで双方の接触面に生じる拡散現象を利用して接合する方法である(3)。MEMSセンサの接合方法として広く使われる技術として知られている。
サファイアセンサチップとNi基合金の金属箔との良好な拡散接合を行うためには以下の3つの主要機能を兼ね備えた接合装置の開発が必要であった。
(1) 1.0×10-5Pa以下の真空度下で材料を保持できるチャンバを持つこと
拡散接合は接触面に発生する拡散現象を利用することから接触面に不純物等があると拡散現象が阻害される。特に加熱時に材料表面に発生する酸化物は重大な阻害要因となるこのためNi基合金の金属箔の酸化を抑制するために高真空下での加熱処理ができる真空チャンバの具備が不可欠となる。
(2) 接合面に一定の圧力を均一に印加できるプレス機構を兼ね備えていること
サファイア隔膜真空計では高い気密性に加え,サファイアセンサチップにひずみなどの影響を与えないために接合面に発生する応力の不均一さを極限まで抑制することが要求される。本装置は生産設備として使用されるため,一度に複数のセンサチップを接合することが必要であり,1つひとつのセンサチップに同一の圧力が印加できる金型も併せて開発された。
(3) 1,000℃以上で熱処理ができる加熱機構を持つこと
サファイアセンサチップとNi基合金の金属箔の拡散接合を生産工程として実現するために,各種の要素技術の開発を進め,この3つの機能を兼ね備えた接合設備を完成させることができた。図11は拡散接合装置の外観を撮影したものである。
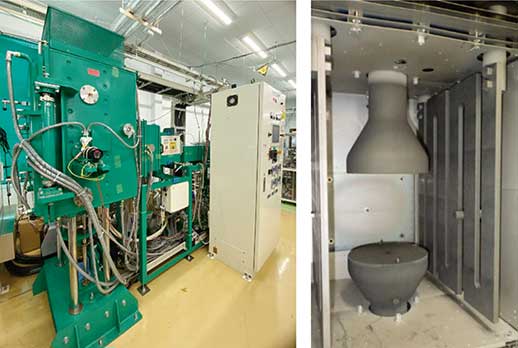
図11 拡散接合装置
拡散接合装置には適正な状態で接合が行われているかを監視する各種のモニタが備わっている。熱処理温度や加圧力はもちろんのこと,前述のように拡散接合の阻害要因となる不純物,コンタミの混入監視を行うガス分析装置が取り付けられており,プロセス中に本来検出されるべきではない元素が検出されていないか,また材料起因の元素もしくは検出されることが妥当である元素であってもプロセスの工程で許容される量を超えての検出がないかを図12のように常時モニタリングしている。これにより拡散接合装置のプロセスが設定された条件どおりに実行されていることを確認することができる。
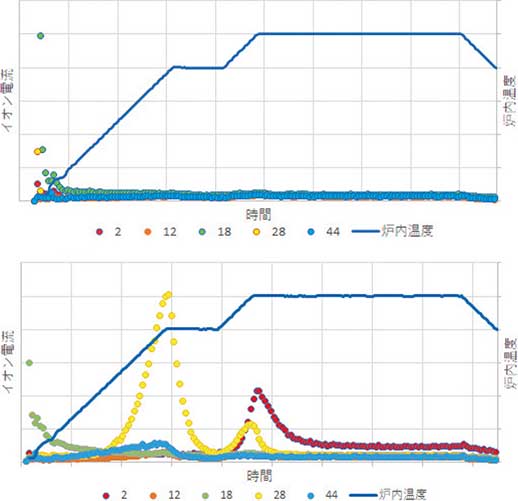
図12 プロセス時のガス分析結果(上:正常時,下:異常時)
3.2.2 高気密性接合の検査工程の確立
拡散接合のプロセス監視により適正な条件下で接合が行われていることを確認できるが,実物での品質検査も不可欠であると考えている。
一般的に高い気密性を検査する方法としてはヘリウムリークディテクタが用いられることが多い。ヘリウムリークディテクタは圧力容器などの内部空間をターボ分子ポンプなどによって真空状態にし,外部からヘリウムを吹きかけ,内部に侵入したヘリウム量を測定することで,リーク量を定量的に計測,評価する方法である。
一方,サファイアセンサチップとNi基合金の金属箔の接合部分は解放された領域の接合であるためヘリウムリークディテクタを使用するためには図7のようなセンサチップを格納する容器となるセンサモジュールまで組み上げる必要がある。しかしこの状態で気密性に不具合が発見された場合は,サファイアセンサチップはもちろんのことセンサパッケージを構成するすべての部品を廃棄しなければならない。生産工程において不具合品を後工程に流出させないということは言うまでもなく鉄則である。
つまり拡散接合工程のあとには,接合の健全性を担保する検査工程を確立することが求められた。ここでアズビルが着目したのは接合部分の光の反射状態の違いである。接合面に光を当て特殊な顕微鏡で観察することで,接合されている部分と,接合されておらず界面にわずかな隙間のある部分では,輝度が異なっているため識別することができる。その一例を,図13に示す。
接合部分を撮影し,その画像データを処理することによって,リークパスの検出だけではなく十分な接合領域が均一に得られているかという接合の質も評価することが可能となった。
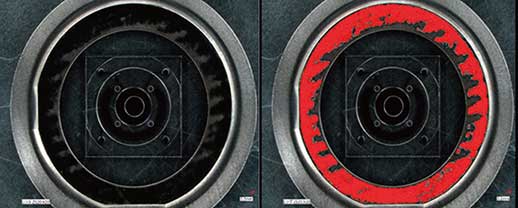
図13 拡散接合面の画像処理による接合評価
この技術開発によって,センサモジュールとして組み上げることなく接合面の気密性検査を行うことができるようになった。
さらにアズビルのセンサモジュール生産工程では,実際の使用環境で長期間使用されても品質を維持できるようにもう1つの検査工程を設けている。この検査は図7のようにセンサモジュールとして組み上げたあと,一定の圧力を持ったアルゴン雰囲気下に一定期間暴露させセンサの出力を計測することで,センサモジュール内部へのアルゴンの侵入がないことを確認している。
この検査では拡散接合面だけではなくNi基合金からなる筐体のすべての接合部分の気密性も確認している。もしわずかにでも気密性が失われた箇所があればセンサパッケージ内部に侵入したアルゴンの影響を受け,サファイアセンサの出力に異常を確認することができる。アズビルがアルゴンエイジング工程と呼ぶこの工程を経ることで,お客さまの過酷な環境下でも長期にわたり安心して使用していただけるサファイア隔膜真空計を提供できている。
このようにセンサパッケージングでは接合などの要素技術の開発だけではなく,その工程の品質を担保するための検査工程の開発も併せて行っていくことが重要である。
4.成果
ピエゾ式圧力センサ,サファイアセンサでの成果について報告する。
4.1 製品化を行う上で不利となるMEMSセンサチップの特性を補完するセンサパッケージング技術
センサへの圧力印加機構の開発により,センサチップの個体差の影響を受けないセンサパッケージングが可能となり,製品仕様を満足する圧力センサの提供が可能となった。
また,接着剤硬化時のプロセス制御による応力除去により,無印加時の出力電圧の安定性を得ることが可能となった。
4.2 MEMSセンサチップの優れた特性を活かすセンサパッケージング技術
サファイアセンサチップの持つ優れた耐食性を活かすために必要なNi基合金の金属箔との良好な拡散接合を行うための要素技術開発,装置開発を行った。
さらには拡散接合の健全性を担保し,次工程に不具合品を流出させないためのプロセス監視,画像処理を活用した接合状態の検査工程に加え,長期使用でも接合品質が維持できることを確認できるアルゴンエイジング工程を確立した。センサパッケージングの要素技術開発と並行して開発されたこれらの複数に重ねられた検査工程によって,過酷な環境下でも長期にわたり使用できるセンサの提供が可能となった。
5.おわりに
アズビルのコアコンピタンスの1つであるMEMSセンサチップのセンサパッケージング技術について報告を行った。
アズビルでは,さらに高感度,高精度なMEMSセンサチップの開発を進めている。それと同時に製品化を行う上で不利となるMEMSセンサチップの特性,優れた特性といった特徴を把握し,それを補完する,また活かすセンサパッケージング技術を開発することにより,アズビルのMEMSセンサチップの持つ優れた特性を最大限に引き出せるように生産技術開発にも取り組んでいる。今後も優れた計測制御機器をお客さまに提供できるように継続的に開発を強化していく。
<参考文献>
(1) 関根正志,石原卓也,差波信雄,谷武夫:サファイア高温隔膜真空計のセンサ素子・パッケージ開発,azbil Technical Review 2011年1月発行号,2011,pp.28-33
(2) 伊奈治,石川智則,成田量一,竹中修:エポキシ樹脂 注型品の硬化プロセス解析技術の開発,デンソーテクニカルレビュー,Vol.4,No.1,1999,pp.94-100
(3) 益本功, 玉置維昭, 寺井清, 永井義夫:拡散接合の最近の進歩,日本金属学会会報, 9巻, 10号,1970, pp.653-665
<商標>
ACTIVALはアズビル株式会社の商標です。
<著者所属>
關 宏治 アズビル株式会社 プロダクションマネジメント本部生産3部
片桐 宗和 アズビル株式会社 技術開発本部マイクロデバイス部
この記事は、技術報告書「azbil Technical Review」の2023年04月に掲載されたものです。
- 2024
- 2023
- 巻頭言:センサなどの製作に用いられる半導体微細加工技術 MEMS
- 特集に寄せて
- アズビルMEMSの歴史と今後の展望
- 小型化,プロセス耐性を高めた サファイアリニューアル真空計の開発
- MEMS技術を駆使して過大圧保護機構を集積化した 超高耐圧差圧センサの開発
- オイルフリー高感度圧力センサの開発と応用検討
- ユーザビリティを向上させた マスフローコントローラの開発
- MEMSセンサの能力を最大限に発揮させる センサパッケージング技術
- 新クリーンルームの設計コンセプト ─ 独創的MEMSセンサの効率的な市場導入促進に向けて
- savic-netTM FX/G5におけるサイバーセキュリティ対応
- 個別快適ニーズに対応するための空調ゾーン細分化技術
- クラウドMESを活用した生産現場における IT基盤の構築とDX推進
- Pharmanage™ Ⅴ 顧客固有の業務プロセスのシステム化を容易にする医薬向けMESの開発
- マルチエリア対応ユーザターミナル(QJ-1201)
- 2022
- 2021
- 2020
- 2019
- 2018
- 2017
- 2016
- 2015
- 2014
- 2013
- 2012
- 2011
- 2009
- 2008
- 2007
- 2006